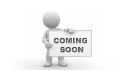
Amr Ahmed Ahmed Elfeky
Cairo University
Egypt
Title: Aerodynamic design of flanged diffuser wind turbine
Biography
Biography: Amr Ahmed Ahmed Elfeky
Abstract
The objective of the current study is to design a flanged diffuser wind turbine for maximum power output. The study starts with the preliminary design of the turbine blades at 10 m/s wind speed and 350 rotational speed using the Blade Element Method to obtain an initial geometry of the turbine in terms of the blade twist and chord distribution along the blade span. NREL S823 and S822 airfoils are used at the turbine blade root and tip, respectively. A numerical investigation is performed to design the diffuser for maximum air speed inside the diffuser. The Numerical investigations are carried out for the flow fields inside the flanged diffuser using the ANSYS FLUENT commercial package based on finite volume method to solve Navier Stokes Equations and the k-ε turbulent model. The numerical investigations are done to study the effect of the diffuser expansion angle, the diffuser length and flange height on the flow field. The velocity contours, static pressure contours and streamlines are presented. 165300 grid cells are used in the study. The results showed that increasing the diffuser expansion angle leads to accelerating the flow through the diffuser when the diffuser angles are between 0° and 12°. After that, the expansion angle effect becomes negligible as the secondary fluid circulation is generated near the end of the diffuser and grows with the expansion angle. Also increasing the diffuser length accelerates the flow entering the diffuser until the diffuser length to inlet diameter ratio L/D reaches a value of 1.25. After that, a recirculation zone is formed at the end of the diffuser. The simulations show that a high pressure region is formed in front of the flange and a low pressure region is generated behind it. The intensity and area coverage of these regions increase as the flange height increases. Thus, the overall flow speed inside the diffuser increases till flange height to diffuser diameter ratio reaches 0.75. The designed diffuser increases the velocity inside the diffuser to 2.2 times the free stream velocity. By studying the load effect on the diffuser it is concluded that the best diffuser load is estimated to be in the range of 0.4 to 0.95. Comparison of the computed results with the experimental data shows good agreement. Finally, the wind turbine is simulated numerically to study the turbine performance with and without the diffuser. The simulations of the free turbine are performed at uniform wind speed of 10m/s. The rotational velocity is assumed to be 350 rpm. A single reference frame model (SRF) is used to simulate the incompressible, steady state flow field. The standard Spalart-Almaras model with Vorticity Based is selected for the turbulence production. 4.5 million structured and unstructured cells are used in the simulation. The results of the numerical simulation are compared with those obtained using the blade element method for the free turbine. The comparisons show good agreement. Numerical simulations of NREL phase II are also performed for the sake of validation of the adopted numerical method. The results show a good agreement with experimental data. Finally, the wind turbine with the flanged diffuser is simulated numerically assuming an inlet wind speed of 5 m/s and 350 rpm. It is found that the power generated increases to five times the power generated by the free wind turbine.