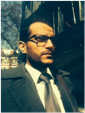
Hamza Alsalla
Exeter University
UK
Title: Effect of different building direction on fracture toughness of ultra high strength aerospace components made by additive manufacturing
Biography
Biography: Hamza Alsalla
Abstract
Direct Metal Laser Sintering (DMLS) and Selective Laser Melting (SLM) are an Additive Manufacturing (AM) technique that produces complex three- dimensional parts by adding layer up on layer of powder materials from bottom to top. Recently, AM has received large amount of press and is set to have a large impact such as decreasing the cost of production, fast and flexible, design freedom, increase the innovation opportunities and develop new materials system for the consumption of Aerospace industries. Since the major problems come across in the process is limited surface quality, and residual porosity in SLM and DMLS parts may be undesirable for some applications where fatigue resistance and high strength are essential. This research aims to improve the fracture toughness, ductility and fatigue life for the metallic components, which is essential to entirely exploit potential of the SLM and DMLS of these alloys for aerospace applications. The development in the Additive Manufacturing technology is not only limited to new machines and new materials and methods but also new processes, to offer high mechanical properties and performance. This research focus on DMLS and SLM of Titanium and Stainless steel alloys to investigate the effect of different building direction on strength, ductility and fracture toughness property. This investigation may create a strong need for a system that could contribution in the selection of the possible process chains, materials and finishing options and may extend the capability of AM process to generate high performance component for commercial application in aerospace industries.