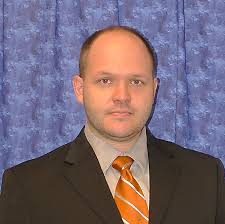
Shawn A. Putnam
University of Central Florida, USA
Title: Heat transfer coefficient characterization in the thermal and hydrodynamic boundary layers of flowing fluids and evaporating thin-films
Biography
Biography: Shawn A. Putnam
Abstract
Transient heat fluxes in cutting-edge computing systems, electro-magnetic switches, and diode-pumped lasers can exceed 50 MW/m2, which is nearly the heat flux radiated by the Sun. To manage extreme thermal loads, the State-of-the-Art is to boil and evaporate liquid coolants on micro- and nano-structured heat sinks. However, modern cooling techniques cannot manage extreme heat fluxes under transient conditions. Thermo-fluid transients due to on/off device operation or system exposure to an extreme environment result in highly unstable thermo-fluid behavior, ultimately placing a liquid-cooled device in danger of catastrophic failure via thermal runaway -- i.e., a rapid, uncontrolled increase in device temperature.
This talk will cover our application of optical pump-probe diagnostics to characterize the local, transient heat transfer coefficient (HTC) in confined geometries: (i) HTC in a developing thermal boundary layer in a microchannel and (ii) HTC in evaporating thin-films. We focus on the heat transfer coefficient because it is the most important thermo-fluid parameter to understand in active, two-phase thermal management applications. Specifically, we use a differential form of the anisotropic Time-Domain Thermoreflectance (TDTR) technique to measure the HTC as a function of fluid flow rate (or Reynolds number, Re) and evaporating thin-film thickness. For example, studies with flowing fluids in microchannels consist consists of single-phase, degassed water flowing in a rectangular microchannel (hydraulic diameter: Dh = 480 µm with local spot heating by the pump TDTR laser beam. Relative to the HTC measured with non-flowing (static) fluids, we find a 30% in the HTC for single-phase water flowing at Re ~ 1800.